Triplex, in-line solventless laminating for more-sustainable, flexible-packaging structures
- Kevin Lifsey
- Mar 7, 2024
- 6 min read
By Eduard Boja, Ph.D., brand mgr.-Lamination & Coating Business Unit, Comexi Group
Abstract
Given the consistent rise in social commitment to use resources with more responsibility and intelligence, regarding the proper gathering and sorting of waste, this firm is particularly dedicated to delivering solutions which are respectful of the environment. Consequently, in regard to mid- and long-term strategies, it is extremely relevant for converting-machinery manufacturers to help develop the next generation of materials and structures. With the installation of this firm’s first tandem-configuration machine for triplex, in-line solventless laminating, which operates solely with monomaterial-based structures, end-users, as well as society, will benefit from more-sustainable and recyclable packaging.
Introduction
This firm has always shown a strong commitment to the environment and the development of machinery that empowers converters to develop and design more-sustainable flexible packaging. However, most of these sustainable materials bring new challenges for the entire packaging supply chain, such as tension control, machinability, printability, barrier properties, sealing temperatures, COF, and a very long list of etceteras.
Taking these challenges into consideration, we have been working toward a number of milestones to facilitate, for our converting customers, the transition from standard materials to those of a new generation of monomaterial structures.
With polyethylene being the driving force, facilitating more recycling and reintroduction of monomaterial structures and solvent-free adhesives into the supply chain are the primary reasons to shift toward these materials. This has compelled many adhesive manufacturers to develop and improve their products, making the final structure easier to recycle, re-extrude, and mostly reusable for non-food applications.
This firm has worked to provide the best solution, be it solvent-based or solvent-free, via intense interaction with adhesive manufacturers, especially focusing on solvent-free adhesives, to ensure that through mutual collaboration, we achieve the best overall packaging performance regarding these types of structures. Due to machinery improvements and new adhesives, monomaterial structures and functional barrier coatings on porous films/paper are at the disposal of converters and their end-user customers. Further, we been able to run solventless triplex laminating in-line, giving converters, if they desire to operate completely solventless laminates, a significant reduction in time.
Solventless-adhesive performance
Solventless adhesives have dramatically evolved over the last few years and are becoming more similar to solvent-based materials, in regard to performance and capabilities, thus making it easier for converters to move away from solvents. Nonetheless, these improvements have bolstered an increase in adhesive viscosity, making it more difficult for these materials to go through the coating unit and be applied properly to the substrates. This is not only especially true for high-performance solventless adhesives but also for many of the new generation adhesives (see Figure 1).

FIGURE 1. Adhesive viscosity by time (in minutes) and viscosity (in mPa*s) at 40° C. for a new-generation adhesive versus a standard adhesive
One of our field-development focuses has been to improve regulation of temperature flexibility in each and every one of the triplex machine’s calenders, regarding both coating and laminating. Systems are now available to reach higher temperatures (up to 130° C.), in the thermoregulator if required, and these units aim to reduce the initial viscosity, particularly for new-generation adhesives.
Driving this flexibility requirement and adhesive improvements, when running triplex solventless, is the need for higher tack during the first lamination. This material needs to remain stable, without lateral slippage throughout the machine, before reaching the rewinder (see Figure 2). Success also has been achieved by lowering the temperature of the first lamination nip. Additionally, we must consider that the surface behavior of these new-generation polyethylene films, even though oriented polyethylene is quite stable, is not as good as what we previously used for other industry standards, such as PET films. Conclusively, complete solventless lamination was achieved at speeds of >250 mpm for triplex structures solely based on polyethene using solventless adhesives, which were specially designed for this purpose.

FIGURE 2. Triplex, in-line solventless laminating line
Solventless lamination plus coating & drying
The second part of our research was being able to run structures consisting of a solventless lamination plus one coating. This was obtained through a machine with triplex configuration using materials solely based on polyethylene, to allow converters to either run full solventless triplex or duplex laminations plus one coating. This configuration requires drying, and consequently presents a considerable challenge regarding the tension control of the material.
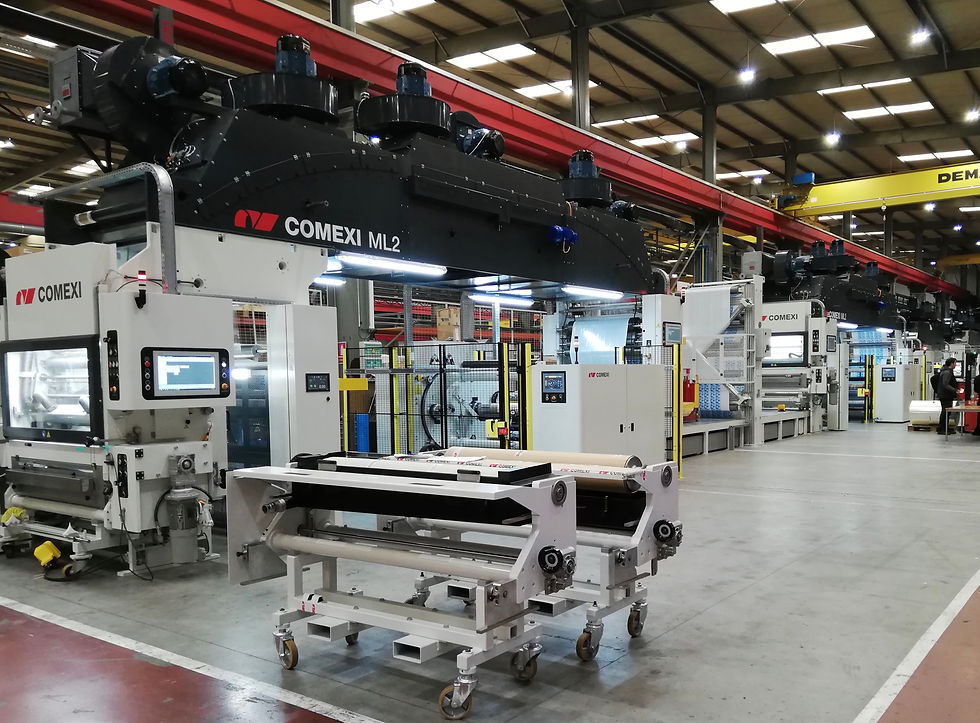
FIGURE 3. Tandem configuration used to test triplex, full-polyethylene solventless and polyethlene lamination with coating
Tension control throughout the machine is most relevant in relation to running full-polyethylene structures, whether or not this is with the use of a triplex configuration. Regarding converting machinery, we could say that oriented polyethylene behaves in a way similar to BOPP film, or at least, it is the most similar material which comes to mind.
This affirmation, however, is mostly valid only when discussing full-solventless applications without the need for drying. Nonetheless, what transpires when we want to run applications such as a duplex-polyethylene lamination plus a coating, be it for esthetic purposes or for barrier, which requires the substrate to go through drying? This can very well be one of the most demanded applications for this type of structure.
Full-PE stretching and shrinking
Accordingly, with full-polyethylene duplex lamination, our primary concerns are lateral stretching and material shrinking. Unless proper airflow and state-of-the-art tension control are used with lower temperatures, the film usually stretches in the opposite direction in which it was stretched during the blown-film process (see Figure 4).
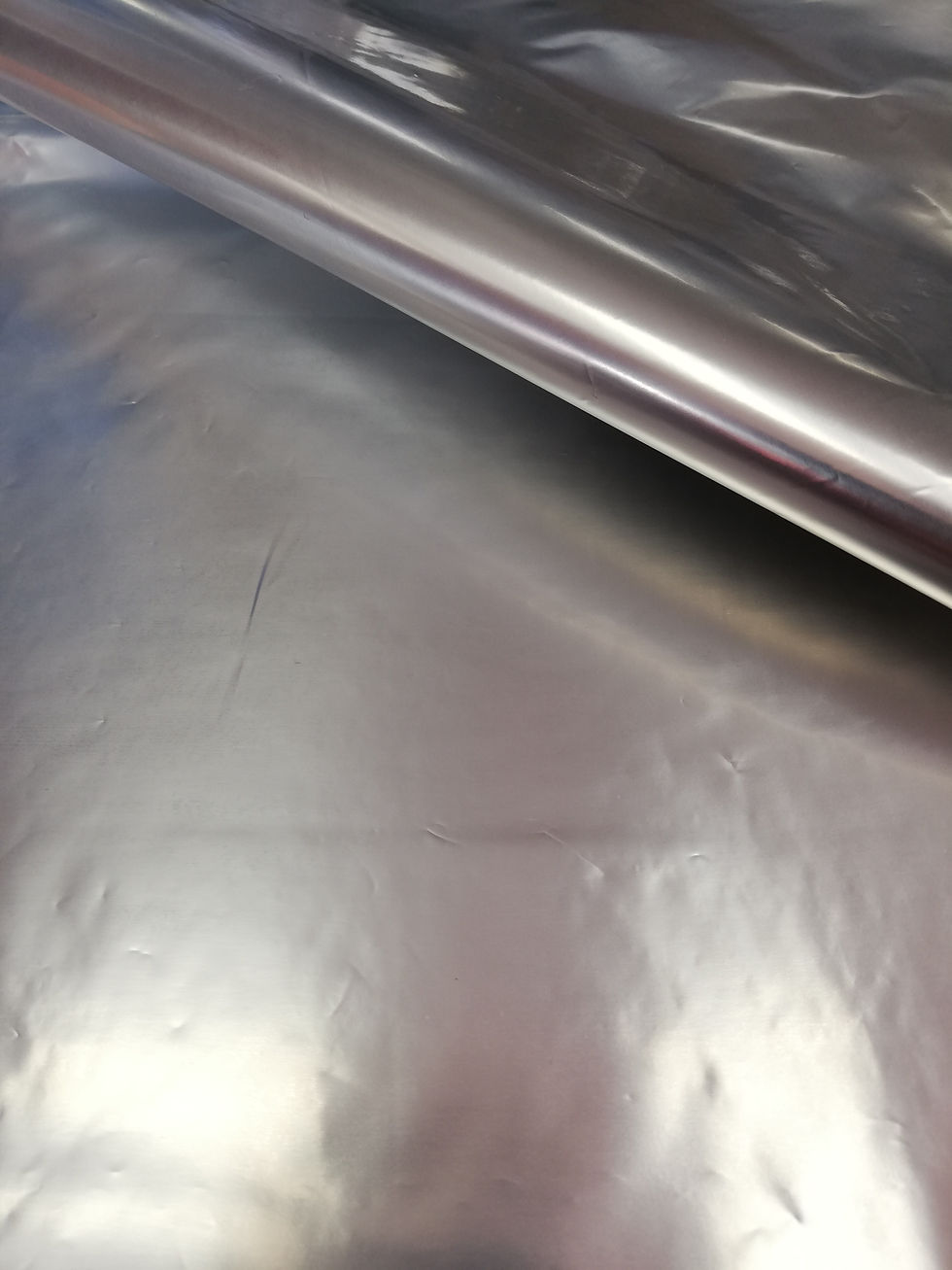
FIGURE 4. A duplex lamination of PE-MDO + metallized-PE MDO
We would call this an accordion effect, due to the type of effect it can have on the film. As the film has been stretched in accordance with the direction of the machine, the effect it has is not like normal polyethylene, because the film orientation retains to a certain extent the lateral extension as well.
FIGURE 5. Illustration of what occurs after excessively heating and overstretching of PE-MDO film
This occurs on irregular lines throughout the film, running from the laterals towards the middle in a somewhat repetitive pattern. This can be avoided with very controlled and precise tension control, as well as through the placement of motorized tunnel rollers and a vacuum roller.
Minor film shrinkage, due to high and unstable drying-tunnel temperatures, is another effect we observed. Some converters attempt to avoid this simply by reducing tunnel temperatures and/or extending the oven drying time of the film, in combination with very smooth tension control and pulling in the laminating nip. Additionally, air flow is a very relevant topic when discussing drying efficiency, and due to significant improvements, we are able to coat over thin LDPE film and efficiently dry it to achieve solvent-free retention without compromising any of the material characteristics.
The conclusions reached: Jobs which use longer drying (a comparison was made between a 6- and 9-meter tunnel) assist in delivering better laminates that avoid stretching. Moreover, relative improvements have been seen when using motorized rollers on the drying tunnel and a vacuum roller at the inlet, which is used on some of the most complex coating machinery.
Conclusion
Overall, sustainability will definitely be the most influential driving force for flexible packaging in the coming years and will affect the way in which most players in the sector, whether they are machinery manufacturers, converters or brand owners, manage their products. Having said this, paper and polyethylene-based solutions appear to have an advantage over other developments and presently seem to be the most viable answers to a claim of sustainability. Regarding full-polyethylene structures, there are certainly challenges in many areas of the converting process to overcome, as we have conveyed throughout this article. Nevertheless, the urge of the flexible packaging world to achieve recyclable structures, and reintroduce them into the supply chain once recycled, will certainly turn the majority of these challenges into established solutions instead in the next few years.
Eduard Boja, brand mgr.-Lamination & Coating Business Unit at Comexi Group (Girona, Spain), holds a Master’s in Engineering/Industrial Management and a Ph.D. in Sustainability, Material Engineering, both from UPC. He has worked in the flexible-packaging sector for his entire career, interacting directly with suppliers and brand owners, on developments in traceability, laser-coding and marking, printing, coating/laminating and slitting. Eduard also holds a Lean Six Sigma Green Belt. He can be reached at +34-627-661-623, email: eduardbojagallart@gmail.com, www.comexi.com
Comments