Lessons learned in advanced “roll-to-part” manufacturing of new consumer-electronics devices
- Kevin Lifsey
- Dec 4, 2023
- 5 min read
Updated: Jan 30, 2024
By Donald J. Davis, head of Technical Services, Kent Displays, Inc.
Those who convert, consume. A key challenge for advanced manufacturers of flexible film: How do consumer expectations impact the R2R process? Through an analysis of one company’s success in converting an unusual technology through advanced “roll-to-part” manufacturing methods into a high-volume, retail consumer-electronics product sold globally, this article outlines key concepts for incorporating an end-consumer focus into optimizing design and production engineering. A five-step protocol driven by listening – customer requirements, feasibility, prototype, scale-up and manufacturing – can help guide converters seeking responsive, agile and innovative ways to make products often, well and quickly to meet dynamic consumer needs.
Editor’s Note: This technical paper expands on the author’s presentation at the ARC Annual Business Summit, held in May 2023 in Greenville, SC. More info: www.rolltoroll.org
Introduction
ur firm, Kent Displays, Inc. (KDI), has been commercializing cholesteric liquid crystal (ChLC) technologies for over three decades. KDI has grown from solely a technology company to a consumer-packaged goods company and beyond through a five-phase plan the results of which include minimal viable products, expanded products to fill niches, a second-generation product to even offering a service-based model where the expertise behind the products is offered as a contracted service for other technologies, converting needs, and manufacturing scale-up.
KDI was founded to commercialize ChLC technology. Even though its early years were spent developing this technology, there always was a strong emphasis on manufacturing. The focus was on liquid-crystal devices requiring simple electrode patterns of metal oxides or conductive polymer – this led to plastic substrates, which led to early interest in roll-to-roll (R2R) processing. KDI applied R2R manufacturing techniques [1-3] to the production of consumer electronics, dramatically reducing manufacturing costs and enabling new products, such as reusable writing surfaces. The company has further advanced the state of the art by introducing a “roll-to- part” process where a near-finished consumer device is made by a R2R converting line. The following describes the story of KDI’s growth through five lessons learned along the way.
1. Advance a core technology
KDI has extensively researched ChLCs and developed various devices and electrical driving schemes. ChLC can be used to make optical devices, displays and writing tablets by placing them in between glass sheets or plastic films. They also can be made bistable (ability to maintain two states/textures); namely, the planar texture – which is reflective – and the focal-conic texture – which is slightly scattering. These two states require no power to maintain them. The reflection band or color of a ChLC can be tuned over a broad wavelength range during the manufacturing process.
If the ChLC is placed between two transparent conductors forming pixels in a passive or active matrix, the pixel can be electrically switched between the two states and information can be conveyed based on the contrast between the states of adjacent pixels.
Additionally, ChLC displays can be optically imaged or addressed to the focal-conic and planar textures. Similar to electrical addressing, these do not need power to maintain the image. The bistable image is created with no patterning of the conductors and offers near-infinite resolution using a patterned light source to produce the image.
In another mode, pressure from a fingernail or stylus can be applied to a display in the focal-conic texture to induce flow of the liquid crystal that relaxes to the planar texture after pressure is removed. The planar texture remains as a mark or writing.
This image is created instantly with no digital lag, creating an inkless, analog-writing device that can be reused by resetting the whole device back to the focal-conic texture using a small electrical pulse.
2. Establish a minimal viable product
A minimal viable product (MVP) is a version of a product with just enough features to be usable by early customers who can provide feedback for future product development. KDI developed its MVP and introduced the reusable Boogie Board® pressure-sensitive writing tablet in 2009. This writing tablet is an all-in-one alternative to single-use paper products and plastic pens and markers. It has the ability to be reused many times with no reoccurring purchases; additionally, the product is mess and clutter-free, allowing for a clean and organized workspace.
3. Grow product offerings based on market feedback
The Boogie Board brand has evolved and grown since its introduction 14 years ago. The line now offers a variety of products ranging from office productivity to kids to home décor (see Figure 1). The brand has experienced 12 years in the retail sector, with over 30 million units sold globally at a combination of mass and specialty retailers (both online and brick-and-mortar locations).

FIGURE 1. Writing-tablet product offerings for kids, education, home décor and office productivity
4. Develop next-generation products
The next step in the evolution of the company’s ChLC products was the launch of VersaNotes™, which now are available commercially across multiple retail outlets (see Figure 2). These small, reusable notes are designed to help keep work and home life organized and color-coordinated. VersaNotes were designed to enhance one’s workspace, enabling individuals to write with anything while mimicking the feel, flexibility and portability of paper. Like the other writing-tablet models, no power is needed to write or maintain the notes, and there are erase electronics incorporated into the writing stylus.
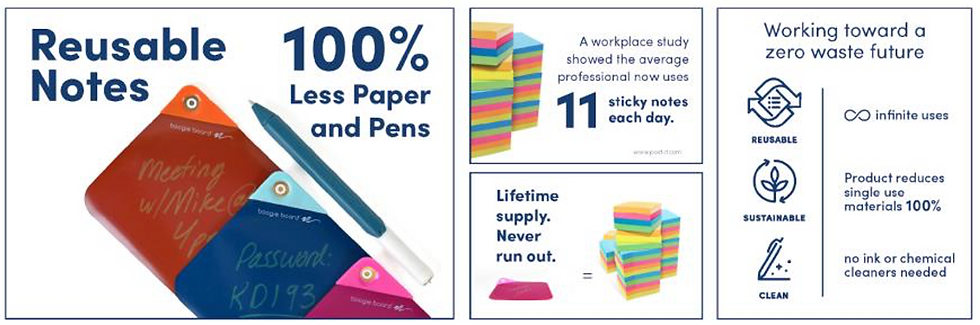
FIGURE 2. VersaNotes’™ rugged, reusable writing surface, which has erase electronics in the stylus, is enabled by roll-to-part manufacturing.
5. Launch service-based model
Our Technical Services business unit offers outside clientele contract-manufacturing and engineering services for other products beyond reusable writing tablets. Cleanroom-based roll-to-roll processing, manufacturing, quality control of flexible LCDs, and fluidic-based optical elements are examples. Technical Services provides engineering, such as circuit design, PCB layout and injection/over-molding part design. Scale-up also can be accompanied, along with process engineering and technical development.
The process involves five steps, beginning with listening. It is important to understand customer requirements and conceptualize the production process. The next step is feasibility, or demonstrating technology made by the compatible R2R process. Third involves the prototyping; this deals in refining the product and the development specifications issued by the customer. The second-to-last step is scaling-up the initial production and problem-solving, followed by the final step: manufacturing. This final step leads to the end result and outflows high-volume production with process and quality control.
It is important that throughout the process as a whole the customer remains the main focus of the operation. In thinking of the end result, keep in mind who the consumers ultimately will be and what their impact will be on the R2R web-processing.
Conclusion
This firm has grown through incorporating the five lessons of 1) advancing a core technology; 2) introducing an MVP; 3) expanding product offerings; 4) introducing next-generation products; and 5) offering a service-based model to the area of advanced roll-to-part manufacturing. By using these five lessons as a model or guide, others in similar manufacturing-related and printed- and flexible-electronics industries can grow their own businesses.
References
1. D. Davis, “Roll-to-Roll Manufacturing of Electronic Writing Tablets,” Converting Quarterly, 2022 Q1, p. 84.
2. E. Montbach and D. Davis, “Roll-to-Roll Manufacturing of Flexible Displays,” in Jehuda Greener, Glen Pearson, and Miko Cakmak (Ed.), Roll-to-Roll Manufacturing: Process Elements and Recent Advances, (pgs. 285-324), New York: John Wiley & Sons, (2018).
3. A. Green, E. Montbach, N. Miller, D. Davis, A. Khan, T. Schneider, J. W. Doane, “Energy Efficient Flexible Reflex™ Displays,” Proc. Intl. Disp. Research Conf., 28, 55 (2008).
Pick up mugshot from original WORD document in Dropbox.
Donald Davis, head of Technical Services at Kent Displays, Inc. (Kent, OH), is a graduate of Oklahoma State University and Thiel College. He holds a Bachelor’s and a Master’s Degree in Physics and his areas of expertise encompass a blend of engineering, manufacturing and business development. In addition to former roles at KDI over the past 17 years, Don has held technical positions at Avery Dennison and Hana Technologies. He also is a Manufacturing Innovation Fellow for the State University of New York at Canton (SUNY Canton). Don is the 2015 recipient of the Visionary Manufacturing Leadership Award and has spoken at conferences such as FLEX, Assn. for Roll-to-Roll Converters Annual Business Summit, ESTECH, and LOPEC. He can be reached at 814-573-8896, email: ddavis@kentdisplays.com, www.kentdisplays.com.
Comments