Ink-viscosity optimization and automation systems for gravure printing and coating: Part 2
- Kevin Lifsey
- Mar 11, 2024
- 7 min read
By Joe Goodbread, Ph.D., chief technology officer; Sunil Kumar, Ph.D., chief executive officer; and Manpreet Dash, markets development and applications engineering, Rheonics
While the latest printing presses are equipped with sophisticated quality control and automation systems, one of the most important variables in printing – ink viscosity – is still typically measured with inexact and cumbersome methods such as efflux cups and falling-ball viscometers. Sensors that measure up to the accuracy operators expect from their color control and press adjustment systems enable on-line, automatic, dynamic control of viscosity within previously unattainable narrow limits, affording start-to-finish maintenance of print quality in even the longest print runs. Using accurate, repeatable viscometers with a responsive control system improves color quality, efficiency, and reduces waste and emissions.
Editor’s Note: Part 1 of this technical paper covered the various challenges of on-line ink viscosity measurement and control.
Gravure challenges
Gravure printing poses special challenges to accurate viscosity measurement and control. Whereas in flexographic-printing systems, cleaning is performed in-line with the printing process, many gravure machines use an off-line cleaning routine. When changing jobs, the ink system is removed from the machine and sent to a wash station where remnants of the previous job’s inks are removed in a device resembling a dishwasher. However, this kind of handling can be rough on viscosity sensors, changing their baseline and even damaging their mechanisms. For machines with removable ink systems, another kind of installation provides a compact, integrated sensor and control valve unit (see Figure 5), which remains on the machine during job changes and is cleaned by an integrated, automated washdown system that removes all traces of the previous ink color from the sensor and associated piping.
A special sensor operating mode can self-test the sensor’s condition, indicating when washdown is complete and also signaling the operator when the sensor becomes contaminated during a printing run. The adapter for mounting the sensors provides for convenient connection points directly in line with the ink pan while providing auto-wash function at the end of the print run.
Complete automation for higher accuracy, reliable and agile printing-process control
Resonant viscosity sensors are often paired with conventional PLC-based control systems. These typically do not make use of all the features available in modern, Industry 4.0-compatible sensor systems. More sophisticated systems can, for example, make use of the highly accurate and reproducible measurements provided by resonant sensors to enable “lock and load” setting of job parameters stored from previous runs of the same job.
One such system of hardware and software offered by this firm enables simultaneous on-line control of ink viscosity on multiple print decks (see Figure 6). All sensors are connected to an industrial-grade computer. The computer controls a valve island, which in turn controls the solvent-dosing valves (see Figure 7). The operator controls the system by means of an intuitive user interface and touchscreen, next to the operator control panel (see Figure 8). The touchscreen displays a dashboard, on which the operator can monitor the viscosity of all stations. Touch-sensitive controls enable the operator to switch individual stations on or off, enable automatic control, and set the viscosity limits. A single dashboard can manage multiple sensors and control valves spread across the factory floor. A separate station hub switches to a display that monitors the viscosity over time and allows adjustment of individual sensors and valves.

FIGURE 5. Adapter for in-line mounting of the sensor and including an auto wash system

FIGURE 6. Real-time ink control is achieved through in-line ink monitoring facilitated by placement of viscosity sensors at each print deck. They connect and transmit data to a central multi-station and single-station handheld consoles.

FIGURE 7. Viscometer installed using a flow adapter, showing the control valves for precise dosing of solvent to regulate ink viscosity.
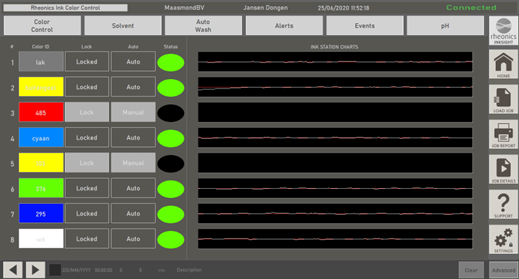
FIGURE 8. Interface screenshot showing an 8-station gravure press with six stations active
Predictive tracking control
During printing there is a continuous loss of solvent due to evaporation, at a rate that increases with increasing printing speed and rising ink temperature. Loss of solvent raises ink viscosity. The sensors update the measurements of ink viscosity and temperature once a second (see Figures 9a-b). This, in turn, enables the controller to determine whether the viscosity falls within the desired range. The controller adds just enough solvent to compensate for deviation of the viscosity from the setpoint. During printing, it is possible to maintain a deviation of only 0.5% from the optimal viscosity. The system uses dosing valves can add the very small amounts of solvent that are necessary to achieve such fine control. The plots in Figures 9a-b are of the same color with different scales, with vertical magenta lines indicating automatic solvent dosing.

FIGURE 9a. Temperature-compensated viscosity (black. 25cP) and temperature (green, ~18° C) vs. time, coarse vertical scale
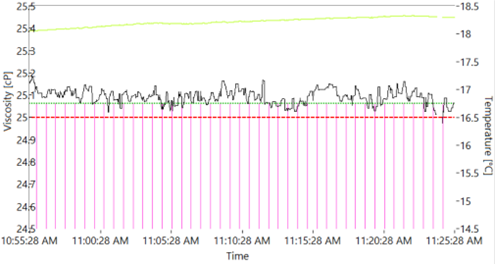
FIGURE 9b. Same plot as 9a, with zoomed-in vertical scale. Temperature-compensated viscosity variation is less than 0.2 mPa.s.
The control system is extremely accurate because it can compensate rapidly and often for the evaporation occurring constantly during printing. To achieve such very small deviations from the setpoint, the system will sometimes dose as little as 10 gm of solvent every 30 seconds.
When fresh ink is added to the ink bucket, its viscosity is intentionally set higher than its final value. The predictive tracking control responds by immediately dosing more solvent, measuring the response to the dose, and repeating until the desired viscosity is reached (see Figure 10). The setpoint is approached gradually with very little overshoot.

FIGURE 10. Response of the system to adding a large volume of cool ink to a system running at 21° C. Note the rapid recovery time of the temperature-compensated viscosity.
Quality assurance, improvement and standardization
An experienced operator knows what viscosity must be maintained for each type of ink in any particular job. Metallic and white inks, for instance, have heavier pigment loading than “normal” inks and present special measurement challenges. Furthermore, the required viscosity also depends on the type of substrate on which the printing is done.
When the ink is too dilute, its viscosity is too low, and the pigment loading is insufficient to give proper color density. When too concentrated, the viscosity is too high, and it tends to produce “pinholing,” which also decreases color density. Accurate initial adjustment of viscosity during setup, and maintaining constant viscosity through the print run, enables more consistent and accurate color density in the printed image. This lets the operator control the final color quality by accurately setting and controlling ink viscosity.
Viscosity control: the key to dE<2 and beyond
Data and insights have enabled the operator to improve color quality and maintain lower and constant dE2000 values, especially during long runs. Tighter viscosity control results in far fewer errors in color-strength deviations in the print-inspection system. Operators who use the systems are able to trust the sensors and control system to provide accurate and repeatable color accuracy. This trust has led to achieving more rapid setup times for small jobs, and consistently excellent print quality for very long runs. And because the sensors need neither maintenance nor recalibration, no further standardization of viscosity values is required beyond the initial setup for each ink. For specific substrates, operators now know what viscosities to maintain. Each new order is stored with the viscosity set values for repeat orders of the same job.
Finally, Figure 11 shows a series of measurements taken from a print job of 24,500 meters, and 13 rolls. The run was interrupted several times, and so was printed on five different days and, in part, at different speeds. Despite the long timespan and interruptions, the dE2000 value never exceeded 1.8.

FIGURE 11. dE2000 for a run of 24,500 meters spread over five days and 13 rolls
Achieving sustainability goals with complete viscosity-automation solutions
Reliable viscosity-automation solutions ensure that only minimal and extremely precise amounts of solvents are used for ink-viscosity adjustments. Table 1 shows how complete viscosity automation helps reach sustainability goals such as reducing waste and setup scrap, and minimizing emissions. When used with an integrated control system and software, records of all solvent additions are kept to enable evaluation and optimization of solvent-consumption pattern (see Table 2). Customers using this firm’s viscosity-automation solutions have reported about a 40% reduction in solvent consumption and total emissions.
TABLE 1. Viscosity automation and sustainability goals
Present and future goals | How complete viscosity automation helps reach those goals |
Sustainability | • Reduced waste and setup scrap lead to lower environmental impact • Precise, targeted solvent dosing • Ability of the balanced resonator viscometers to work reliably and repeatably at any viscosity means these viscometers support transition from solvent-based to water-based inks |
Compliance | • Accurate dosing of solvents ensures minimal, precise amounts of solvents are consumed, leading to reduced emissions • Less scrap, waste and rejects to dispose |
TABLE 2. Solvent consumption and emissions data reported by a customer in printing industry after commissioning of SRV viscometers and controller

Notes:
[1] Proprietary viscosity-automation solution commissioned on printing-press ink stations in June 2018
[2] Second system commissioned on laminator in April 2020
Conclusion
As printing speeds increase, and profit margins get tighter, “getting it right the first time” for each job becomes much more important. Tight viscosity control with an accurate sensor combined with a responsive control system enables gravure printers and coaters to streamline process while improving color quality and reducing waste.
Joe Goodbread, chief technology officer at Rheonics (Winterthur, Switzerland), holds a B.S. in Aerospace and Mechanical Engineering Science from Princeton University, an M.S. in Biomechanics from Stanford University, and a Ph.D. of Technical Science in Biomechanics from ETH Zurich. He is a founding member of the team that developed the firm’s core technologies over the past 30 years. Joe established and directed the Experimental Mechanics Laboratory at the Institute for Mechanics, ETH Zurich. He has developed substantial IP in the field of fluid-properties sensors with 11 granted patents and several more pending. Joe can be reached at +41-78-735-1273, email: joe.goodbread@rheonics.com, https://rheonics.com
Sunil Kumar, chief executive officer at Rheonics, holds a Bachelor’s in Aerospace from the Indian Institute of Technology, Kharagpur, a Master’s in Mechanical Engineering from the University of California, Irvine, and a Ph.D in Electrical Engineering from Imperial College, London, where he developed the Seis-SP seismometer that is part of the main payload for the NASA Insight mission to Mars. He has extensive experience in the sensors and energy sector, having worked in a variety of roles in engineering and research in his early career. Most recently, Sunil worked at Baker Hughes, where he led global engineering for drilling services. He can be reached at +41-52-511-3203, email: sunil.kumar@rheonics.com
Manpreet Dash leads the markets development and applications engineering team at Rheonics. He holds a Bachelor’s in Mechanical Engineering and a Master’s in Industrial and Systems Engineering (Dual Degree) from the Indian Institute of Technology, Kharagpur. During his studies, he worked on developing fluid-characterization models in thermal spray-process applications. Manpreet co-founded the IIT Kharagpur Young Innovators Program and is a recipient of the Institute Silver Medal. He can be reached at +91-99339-40602, email: m.dash@rheonics.com
Comments